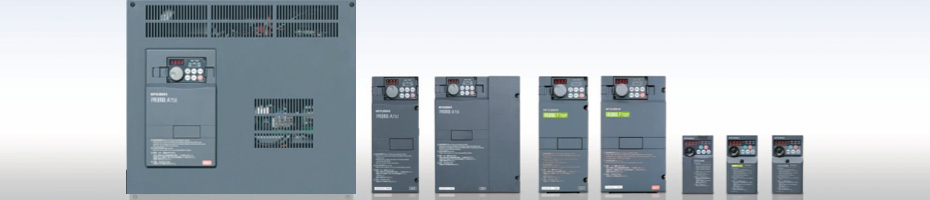
Mitsubishi FR-A700 Series
Advanced functionality and high-performance inverter
Features
Pursuing the best performance
- High-accuracy, high-response speed control using vector control is possible with a general-purpose motor without encoder. (200% 0.3Hz (3.7K or lower), with Real sensorless vector control)
Torque control and torque limit under speed control is possible. - Full-scale vector control is possible by using this inverter with a motor with encoder. (When using optional FR-A7AP or A7AL)
In addition to zero-speed control and servo lock, torque control and position control are available with this general-purpose inverter.
The speed command response is improved. (Speed response 300rad/s, speed control range 1:1500 (with model adaptive speed control))
The torque fluctuation caused by changes in the motor temperature is reduced. (With adaptive magnetic flux observer having ±5% repeated torque accuracy)
The speed control gain and position loop gain do not need to be adjusted. (When simple gain tuning is set.)
Improved reliability and easy maintenance
- The lives of the cooling fan and capacitor have been extended.
- Using the self-diagnosis function, the part life warning can be output and the degree of deterioration can be monitored to prevent malfunction.
- The removable control terminal block and the cooling fan cassette make it easy to replace.
Environmentally friendly
- The newly developed built-in EMC filter reduces electromagnetic noise generated from the inverter.
Easy-to-use
- The machine analyzer function of the FR Configurator vibrates the motor to analyze the resonance frequency of the machine. The notch filter function is available to avoid machine resonances.
- Encoder expandability
The power voltage and input circuit can be selected according to the encoder. (Differential line driver/ complementary, separate power supply (5/12/15/24V) required.)
Model
Specifications
Control method | Soft-PWM control, high carrier frequency PWM control (V/F control, Advanced magnetic flux vector control or Real sensorless vector control can be selected) Vector control *1 | |||||||||||||
---|---|---|---|---|---|---|---|---|---|---|---|---|---|---|
Starting torque | 200% 0.3Hz (0.4K to 3.7K) 150% 0.3Hz (5.5K or higher) with Real sensorless vector control or vector control *1 | |||||||||||||
Output frequency range | 0.2 to 400Hz (Up to 120Hz with Real sensorless vector control or vector control *1) | |||||||||||||
Regenerative braking torque |
Maximum value/ permissible duty |
|
||||||||||||
Acceleration/deceleration time setting | 0 to 3600s (up to three types of accelerations and decelerations can be set individually.) | |||||||||||||
Multi-speed | 15 speeds | |||||||||||||
Speed command | 0 to 5VDC, 0 to 10VDC, 0 to ±5VDC, 0 to ±10VDC, 4 to 20mA, digitally set with pulse train input, operation panel or parameter unit, 4-digit BCD or 16-bit binary (when using optional FR-A7AX) | |||||||||||||
Alarm output | 1 changeover contact (230VAC, 0.3A, 30VDC, 0.3A), open collector output, alarm code (4-bit) output | |||||||||||||
Output signal | Five types of open collector outputs and two types of contact output (1 changeover contact) can be selected from inverter running, up to frequency, instantaneous power failure (undervoltage), frequency detection, operation ready, overload warning, error output and alarm, etc. | |||||||||||||
Monitor function | One type can be selected from output frequency, motor current (steady or peak value), output voltage, operation speed, motor torque, converter output voltage, regenerative brake duty, input power, output power and load meter, etc. Pulse train output (1440 pulses/s 2mA) and analog output (0 to 10VDC) | |||||||||||||
Restart after instantaneous power failure | Available (reduced voltage method (frequency search selectable)) | |||||||||||||
Removable terminal block | Used for control circuit terminals | |||||||||||||
Communication function | RS-485 supported (Modbus-RTU) as standard, CC-Link, PROFIBUS-DP, DeviceNetTM, LONWORKS®, SSCNET III, and FL remote options available |
*1: Available when an option (FR-A7AP/FR-A7AL) is mounted.
*2: The following performance can be attained when FR-ABR (option) is connected: 150% torque and 10%ED for 0.4K and 0.75K, 100% torque and 10%ED for 1.5K to 7.5K, 100% torque and 6%ED for 11K to 22K.
*3: The following performance can be attained when FR-ABR-H (option) is connected: 100% torque and 10%ED for 0.4K and 0.75K, 100% torque and 6%ED for 11K to 22K.